Camera-based inspection systems with artificial intelligence enable product quality control at a level that previously could only be performed by humans. This article explains how and why to use AI in your production and how PEKAT VISION can help you.
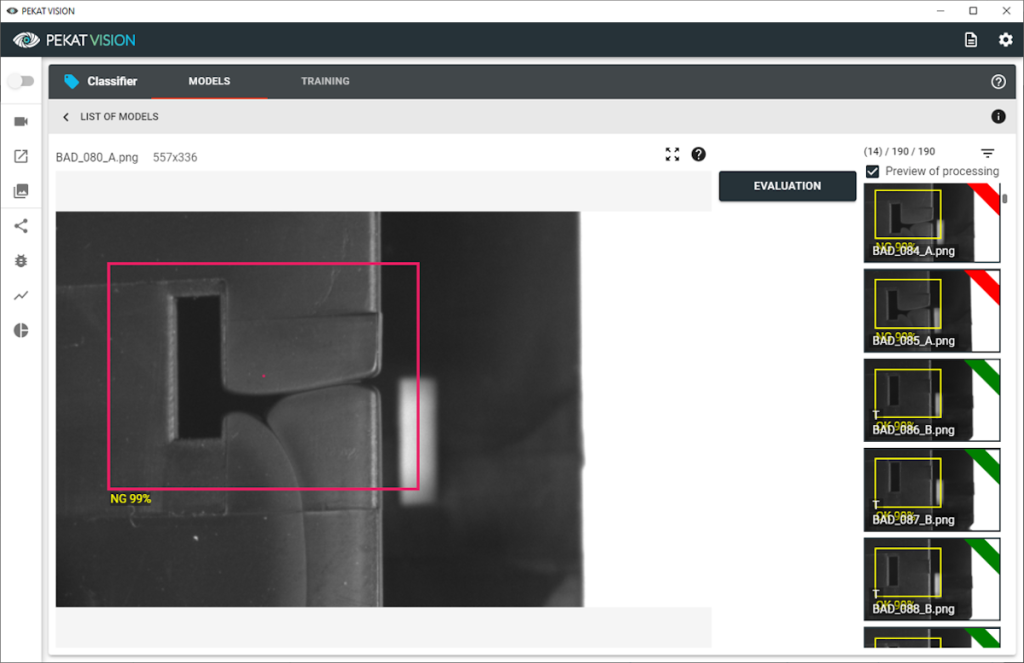
The goal of deploying an automated visual inspection is to increase inspection reliability and reduce overall production costs compared to human inspection:
- Reduction of personnel costs
There is no need to have a product inspection person at each machine at all times. On the contrary, one worker can check multiple stations and react only when needed. - Reduction of scrap rate
The specifics of the human vision is well known. The main advantage of using automated visual inspection is that the algorithm evaluates the products in the same way. Even though some inspections may not be 100% accurate, in most cases the reliability is considerably higher than that of human inspection. Vision inspection provides traceability of products when needed. - User experience
Training the AI involves the user presenting it with images that show certain defects or objects that need to be found. Thanks to its user-friendly interface, neural network learning can be performed by a trained worker without deep knowledge of image processing algorithms.
Vision inspection tasks with PEKAT VISION
Several types of camera inspection can be carried out on plastic products:
- Inspection of short moulds, shrinkage, burrs and other shape defects
- Surface quality inspection: scratches, cracks, dents, texture change
- Inspection of painted parts: orange peel, scratches, dust, unpainted areas
- Detection of components, metal parts, connectors, etc.
- OCR/OCV – Reading and verification of texts, dates and symbols
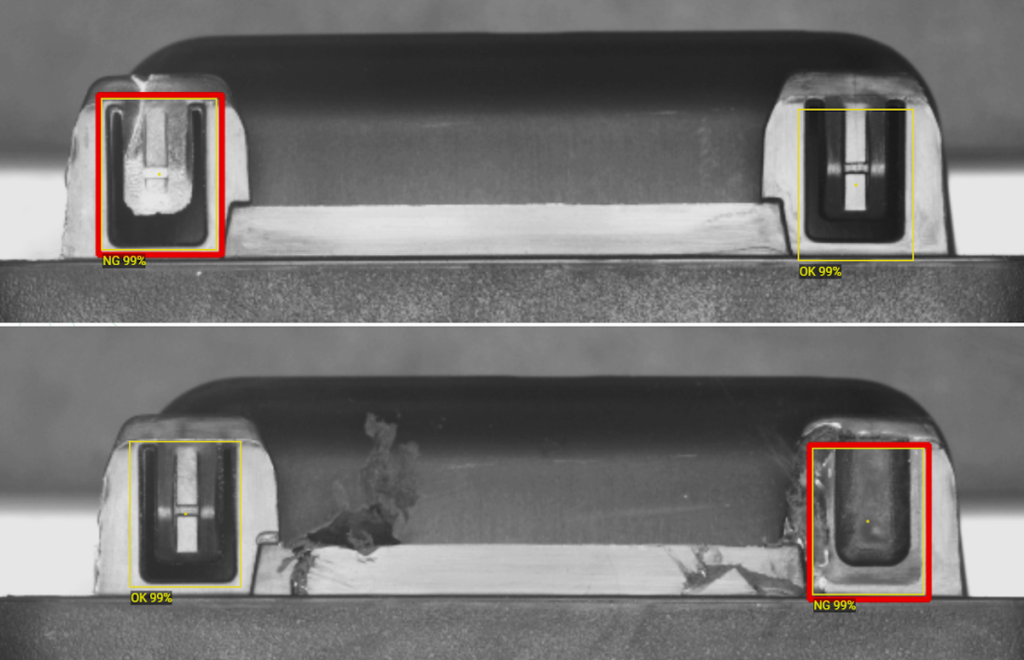
How can a visual inspection system look in practice?
The specific implementation depends on the size of the product and the type of defects to be inspected. Let’s take an example of injection moulding and part inspection: many injection moulding machines are equipped with a manipulator or robot that removes parts from the mould. In its route, the manipulator passes through a place where a camera system is installed. As the manipulator moves, the parts are photographed, the images are transferred to a computer and evaluated so that the parts can be sorted by the manipulator.
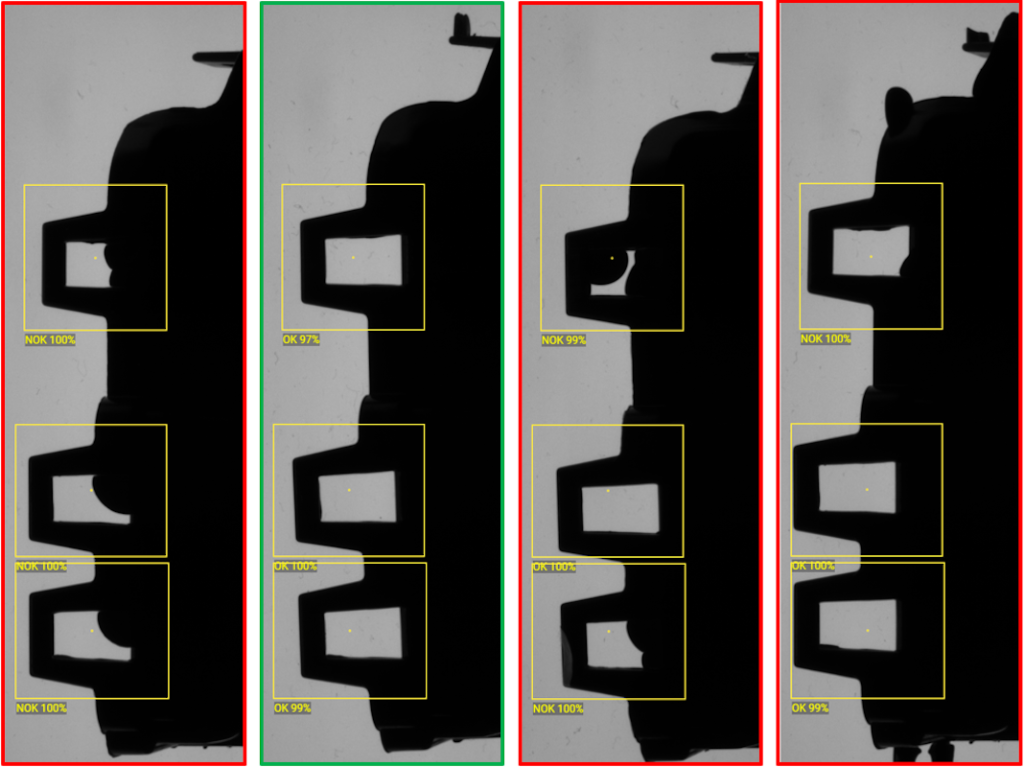
Parts can also be scanned on a conveyor or in a jig, for example when the task is to check the quality of a polished or painted surface. In this case, the product passes through a light tunnel or under a ramp with cameras that can capture even very subtle differences by reflection, as shown in the following figure.
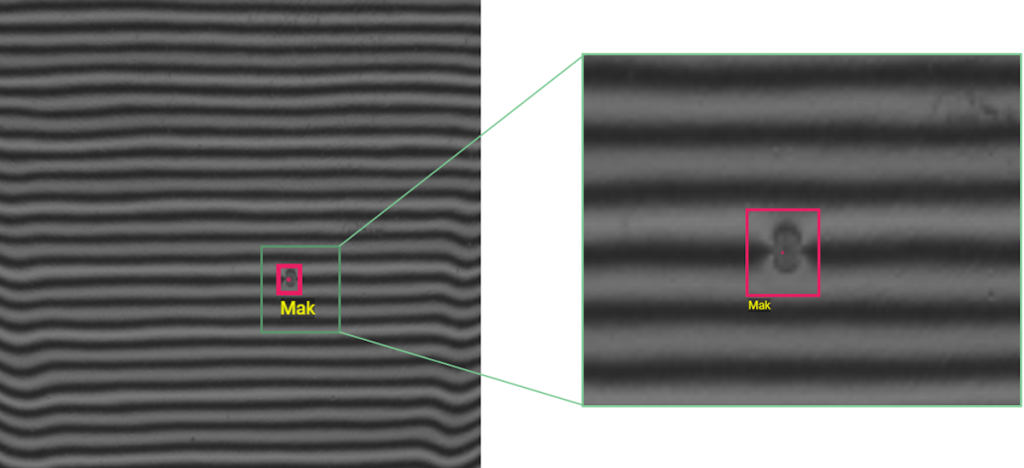
Specifics of AI camera control
Conventional algorithmic image processing can measure the dimensions and exact shape of products, but often cannot detect various-looking defects and anomalies. An artificial intelligence system detects defects and product features as an expert eye would judge them, but it is not suited to precise measurements. In practice, a combination of both approaches is used to create very reliable visual inspection of products.
Compared to standard image processing methods that run on normal computers, AI usually requires parallel data processing. For this, processors on graphics cards are used. The hardware costs are thus slightly higher, but this is offset by the functionality of the software, which can solve algorithmically infeasible tasks.
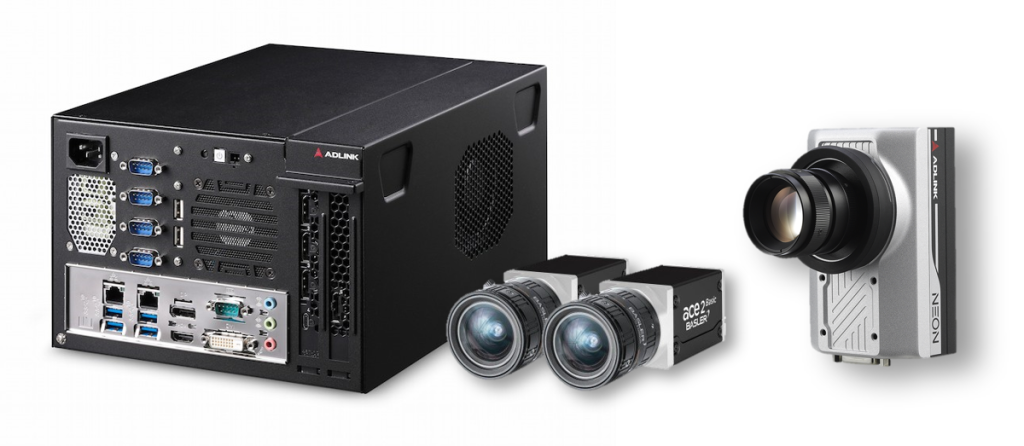
When automated camera inspection is appropriate and when it is not
The advantage of camera inspection is high reliability and repeatability in cases where products manufactured in large batches are routinely inspected. It is limited or impossible to use in cases where it is not possible to ensure the positioning of the part relative to the camera or where lighting conditions are unstable. It is also worth considering for use in inspecting shape-complex products where multiple cameras are required, or to manipulate the product with a robot in front of the camera (the problem is usually the cost of the robot cell and the excessive stroke time). On the other hand, it is very suitable for use in cases where products are inspected at high stroke rates (units to tens of products per second).
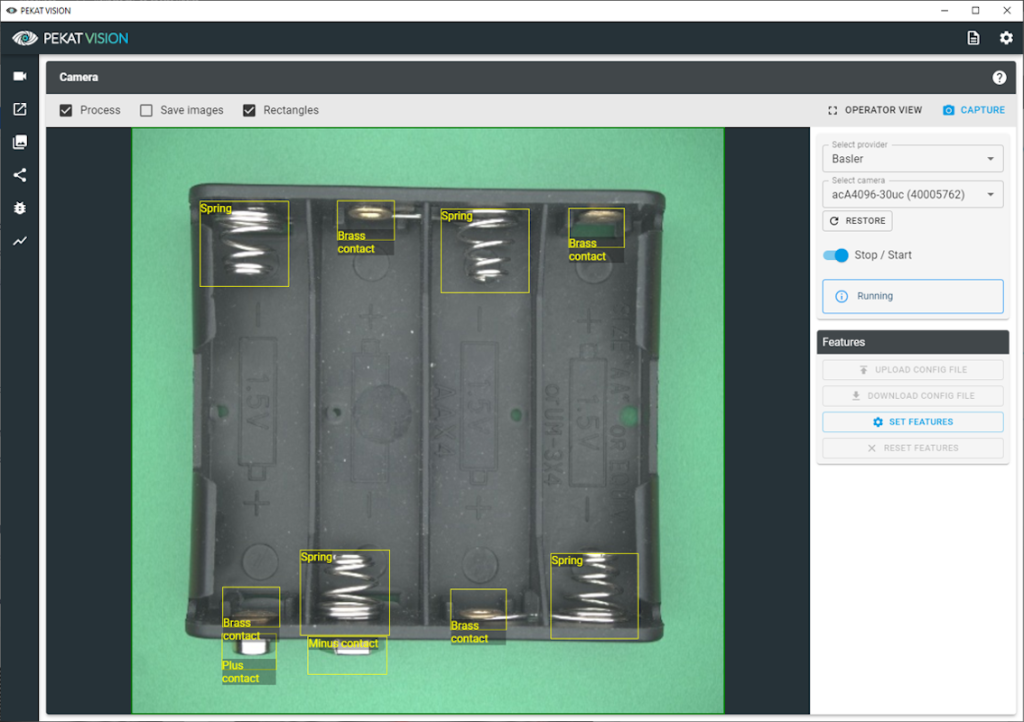
Is PEKAT VISION suitable for my operation?
Although the principles of artificial intelligence have long been known and widely popularized, it is still a novelty in industrial applications. Therefore, PEKAT s.r.o. verifies the functionality and reliability of the artificial intelligence system directly on products or customer images. Of course, feasibility studies and system loans are carried out prior to live deployment. The service also includes the design of the optical part of the system and related hardware.
How to try PEKAT VISION software?
The PEKAT VISION software itself can be tested for free by requesting a demo. However, testing the system directly in operation requires some experience and camera equipment. PEKAT s.r.o. provides consultation to system integrators and end users and actively assists them in testing and deploying the system directly in production. Contact us!
Artificial Intelligence
The term artificial intelligence (AI) is used to describe a data processing principle in which instead of programming a complex algorithm ourselves, we let it be created inside a neural network using the principle of deep learning. To train a neural network in PEKAT VISION, it is usually necessary to acquire tens to hundreds of images of OK and NOK products.
What is PEKAT VISION?
PEKAT VISION is a software for visual inspection of products using neural network and deep learning methods. It is designed for use in industrial applications where quick deployment and easy configuration by an application engineer or process engineer is a priority without the need for deep knowledge of artificial intelligence principles. PEKAT VISION can detect anomalies, inspect surfaces, search and classify objects, read text and symbols on products.