Identifying surface defects on reflective materials is a major challenge in industrial quality inspection. Regardless of the material or defect type—scratches, dents, bumps, inclusions, or paint defects—they can be easily overlooked under standard lighting conditions. Reflections and uniform illumination often mask subtle imperfections.
To improve surface defect detection on plastic light switches, we recently tested the use of a programmable patterned light in combination with the PEKAT VISION Detector module.
Challenges in Detecting Defects on Reflective Surfaces
Plastic light switches often have a smooth, glossy, or semi-glossy surface, making it difficult to detect minor defects like scratches and dents. Traditional illumination methods may fail to highlight surface variations, leading to missed defects.
Patterned lighting offers a potential solution by casting structured illumination onto the surface, enhancing defect visibility.
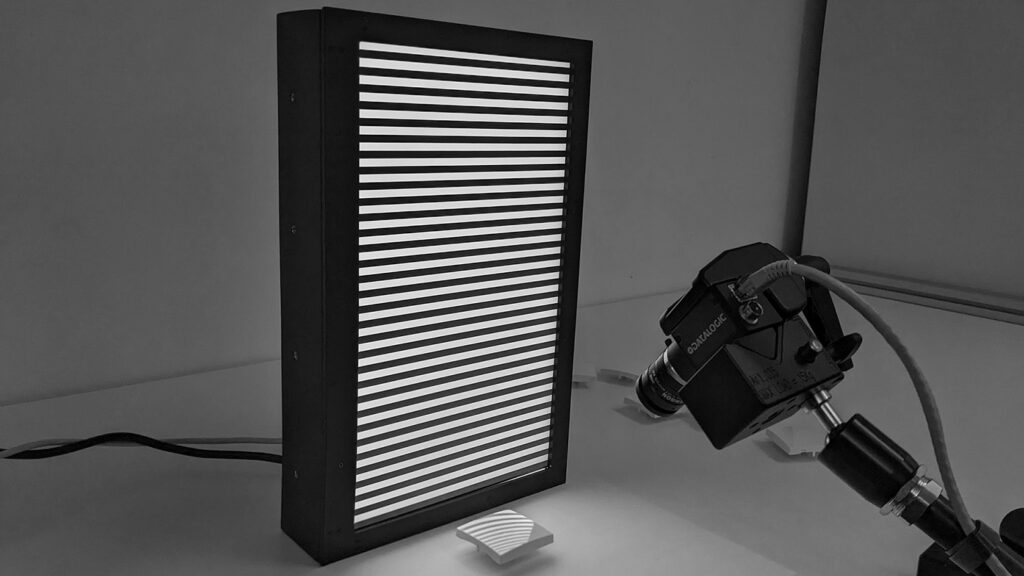
Optimizing Inspection Setup for Glossy Materials
For our experiment, we used a programmable light source, the OPT-PCP, capable of projecting various structured patterns. We configured it to emit:
- Horizontal stripes (two different thicknesses)
- Vertical stripes
The light switches were placed on a desk at a 90-degree angle to the light, while the camera was positioned at a 45-degree angle opposite the light source (Image 1).
The Detector module was trained to identify two common surface defects found on light switches and other glossy plastic surfaces:
- Dents
- Scratches
Improving Defect Visibility with Patterned Light
The patterned light was reflected off the switches, captured by the camera, and processed by PEKAT VISION in real time. The results showed how different defect types interact with structured light:
- Scratches create contrast between the scratch and the switch’s surface (Image 2a).
- Dents distort the otherwise straight patterns (Image 2b).
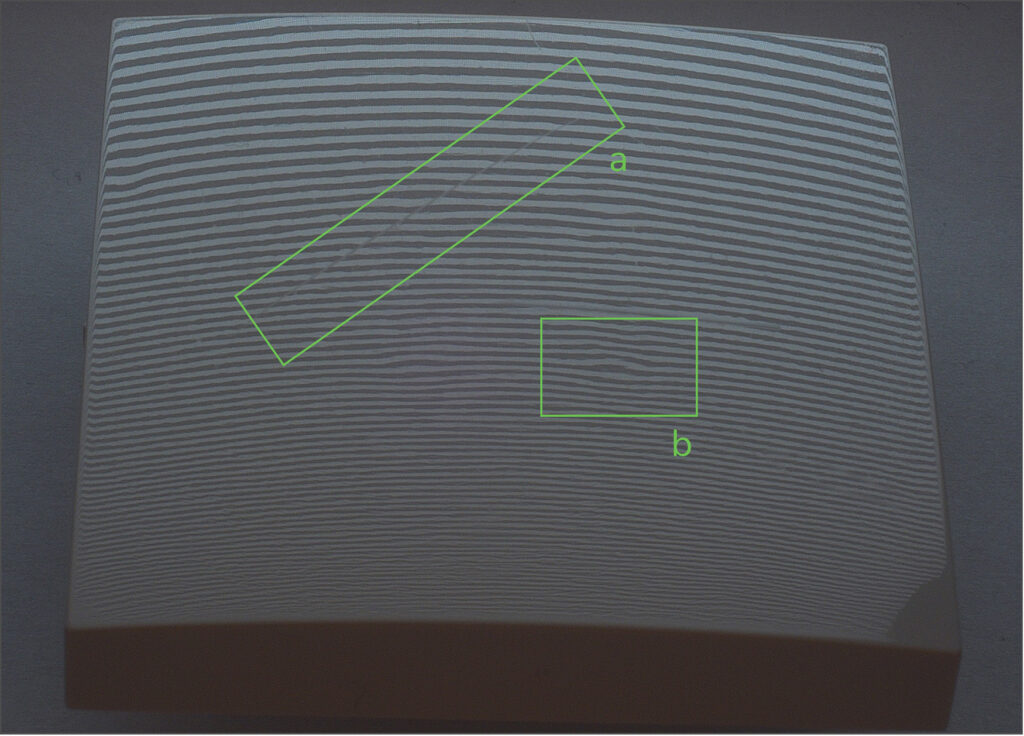
This experiment demonstrated the effectiveness of patterned illumination but also revealed a limitation of using only one pattern orientation. Some scratches were undetectable under horizontal patterns, regardless of stripe thickness. Since the scratches aligned with the pattern direction, they were essentially masked (Image 3). However, when vertical stripes were applied, these scratches became clearly visible (Image 4). Conversely, using only vertical stripes resulted in some small dents being missed (Image 4).
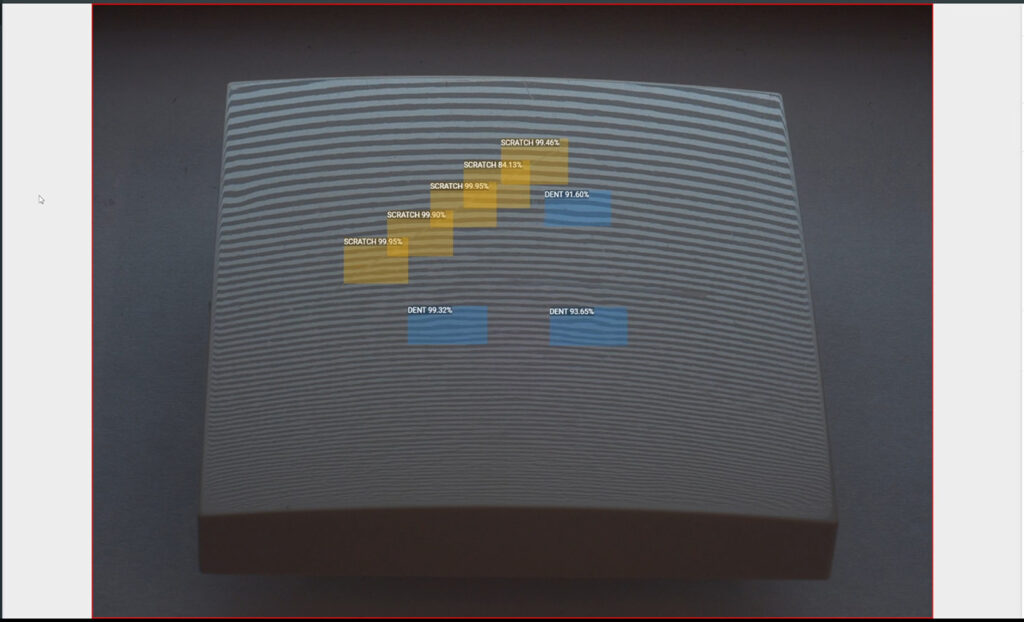
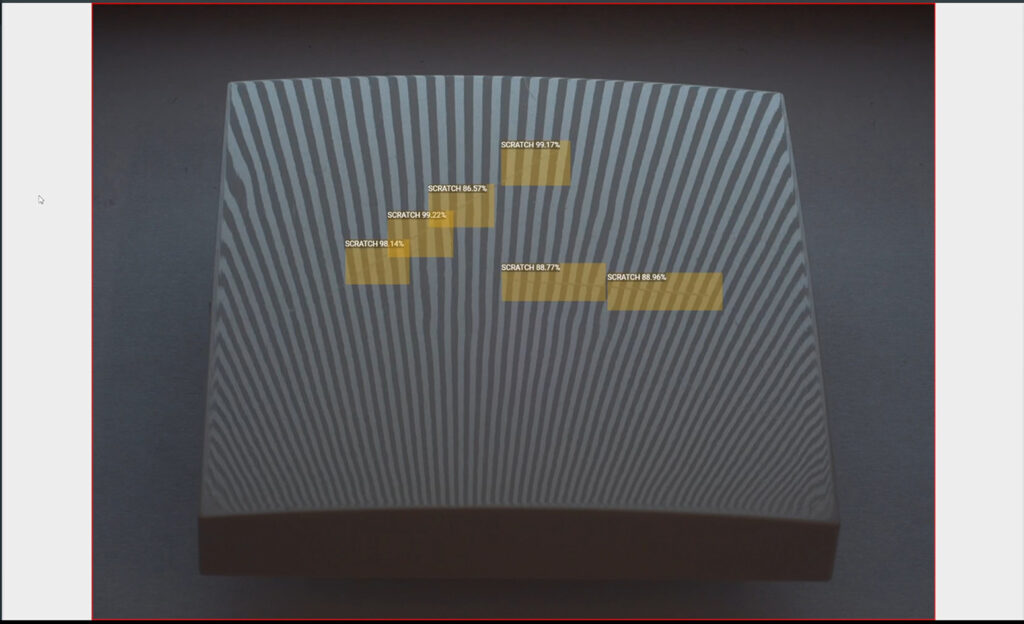
By cycling between horizontal and vertical patterns, the PEKAT VISION Detector module successfully identified all defects, reinforcing the importance of selecting the right illumination for defect detection—in our case, the combination of horizontal and vertical patterns.
The experiment also showed that stripe thickness had minimal impact on defect visibility. In only a few cases, small dents (due to their relative size) were detected exclusively under the thinner patterns (Image 5).
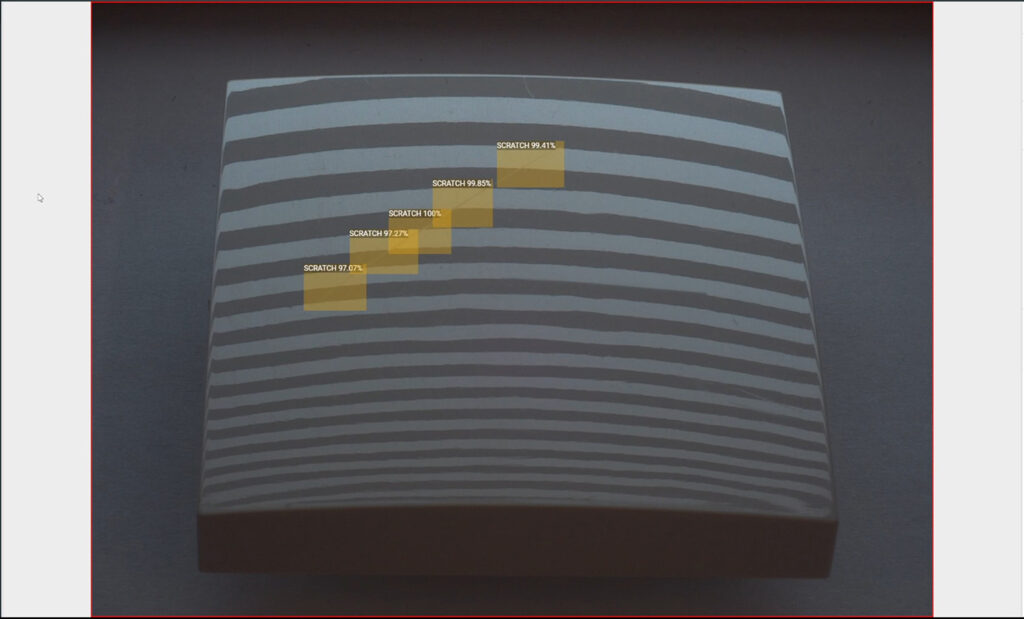
However, different applications may require specific pattern types and thicknesses to effectively highlight defects of varying sizes and characteristics.
Other Applications of Patterned Light
Patterned light is widely used in the automotive industry to inspect painted or coated surfaces. In one of our previous use cases, we demonstrated its use in car hood surface inspection. The PEKAT VISION Surface Detection module precisely highlighted scratches, dust, varnish defects, and other surface irregularities using a heatmap visualization.
In another use case, we examined quality inspection of transparent materials, specifically drinking glasses. By using patterned backlighting with the glass placed between the light and the camera, our software detected cracks, scratches, material inhomogeneity, and inclusions (foreign objects in the glass).
Advantages of Programmable Patterned Lighting
A key advantage of programmable lighting is adaptability. By adjusting:
- Stripe thickness
- Pattern direction
- Illumination/pattern type
…we can optimize defect visibility for different materials, surface types, and applications. This flexibility makes programmable lighting a valuable tool for industries requiring precise surface inspection, such as automotive, plastics manufacturing, and metal processing.
Conclusion
Our experiment confirms that patterned illumination significantly enhances defect detection on glossy and reflective surfaces. When combined with PEKAT VISION’s deep learning software, it provides a reliable, automated quality control solution for challenging inspection tasks.
It substantiated that proper illumination is crucial for each specific application. We understand that choosing the right setup—including lighting, inspection sequences, and AI modules—can be overwhelming for companies new to machine vision and automated defect detection.
Request a Free Feasibility Study
To help manufacturers find the best solution, we offer a free feasibility study. Our team will:
- Determine whether AI-based inspection is suitable for your application.
- Recommend the best PEKAT VISION AI modules for your needs.
- Advise on the ideal inspection setup, including lighting and sequencing.
Contact us today to request your free feasibility study! Let our experts tailor a solution to your specific application needs.