PEKAT VISION, part of Datalogic Group, specializes in the development of software for visual quality control in production environments based on artificial intelligence. Since its establishment in 2017, it has been a pioneer in this field.
The PEKAT VISION application is designed for easy deployment by an application engineer with no programming knowledge. Based on advanced deep learning algorithms and neural networks, the application consists of a module for anomaly detection, object detection and classification, surface quality control and character and symbol reading OCR.
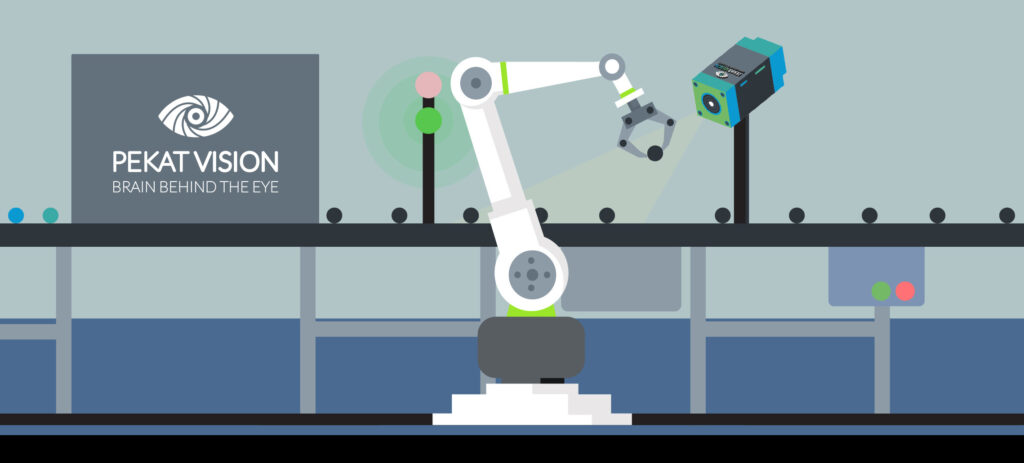
Traditional Quality Inspection
In practice, quality control systems often use a stationary camera focused on the conveyor belt. If a component passes on the belt and is deemed defective based on the camera image, the software sends the information to the PLC controlling the conveyor belt. The component is then automatically removed or, in some cases, the entire belt is stopped and an operator is notified. Camera inspection offers high reliability, especially when inspecting products produced in large batches and at high speeds.
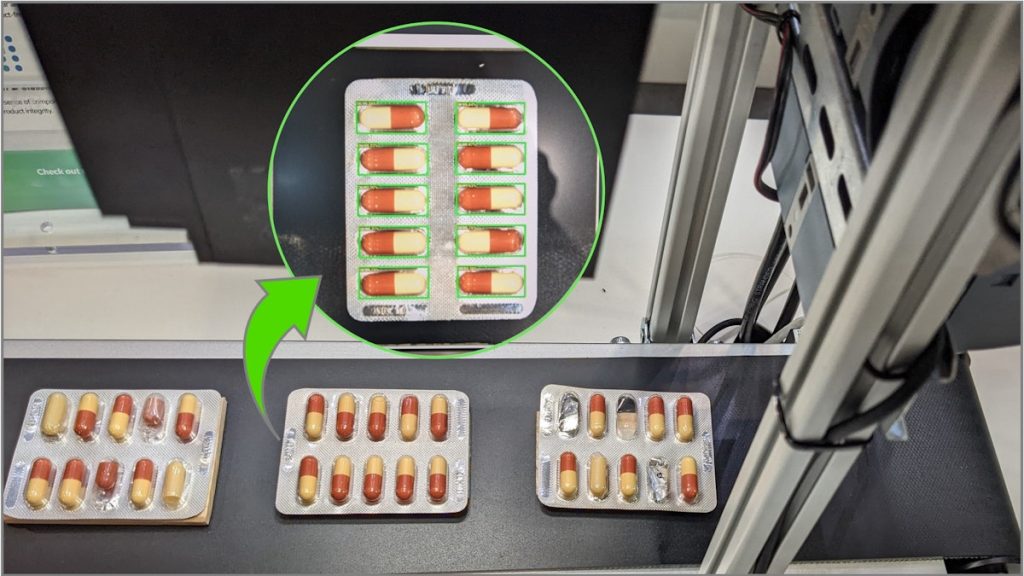
A Cobot Comes to the Rescue
However, when inspecting complex or larger products, using a larger number of cameras or manipulating the product in front of the camera with a robot may be necessary. Collaborative robots, or cobots, have significantly reduced the cost of creating automated workstation. Cobots can work directly with employees without the bulky safety enclosures. Their built-in safety systems allow them to be stopped when they come into contact with an employee. Collaborative robots are versatile, easy to set up, repeatable, and affordable.
Fully automated quality inspection of even complex or larger products has thus become commercially viable for a large number of companies. Like PEKAT VISION’s products, collaborative robots are designed for companies of almost any size and require a minimum level of technical expertise to deploy them in production.
Multiple Viewpoints
Using a collaborative robot for quality inspection allows for manipulation of the part being inspected in front of a camera and viewing it from multiple sides or angles. Providing images of inspected parts from multiple angles is particularly useful when inspecting smooth, shiny, often large surfaces, looking for surface defects such as various scratches, cracks, dents or blemishes.
This approach allows for a comprehensive inspection and the capture of detailed images that would otherwise require the involvement of multiple cameras to capture images from multiple angles and worker intervention to rotate the part for inspection from both sides.
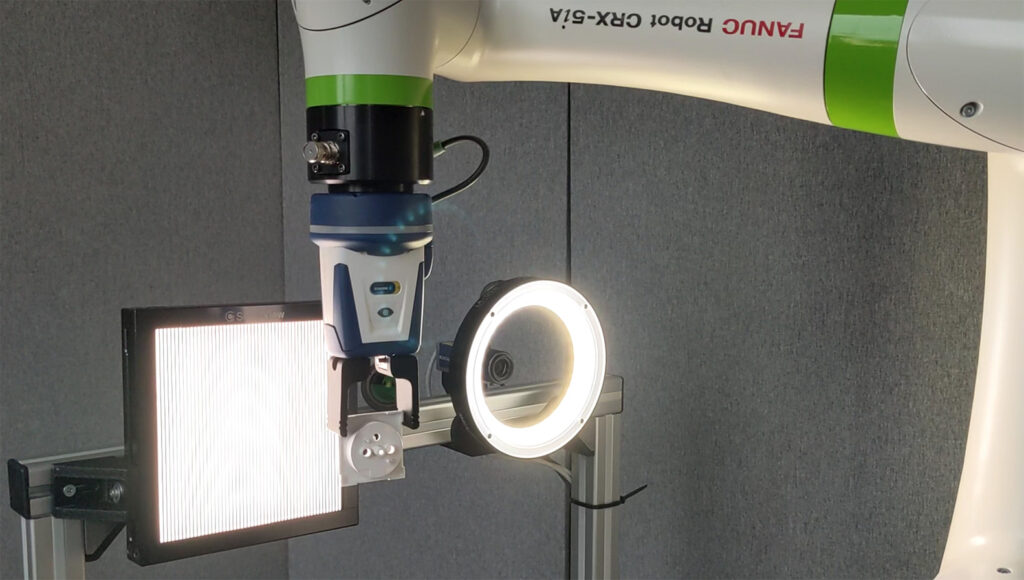
For the Robots 2024 event, PEKAT VISION showcased plastic sockets to illustrate practical inspection methods. Although this demonstration may not entirely reflect the high production rate of plastic sockets, it effectively showcased the inspection process.
Quality Control of Plastic Parts
The outcome of plastic injection molding is affected by a number of factors, including the choice of raw materials, mold quality, pressure, temperature, injection speed and other factors. This can lead to a number of defects including spots, burrs, inclusions, voids, cracks or incomplete mold filling.
In the example presented at Robots 2024, the PEKAT VISION software identified various surface defects on the front, shiny sides of the sockets, and incomplete parts on the back sides. On the front sides, there were mainly scratches that could have been caused by handling the sockets, and on the back sides, the lack of material of the protruding parts caused by incomplete mold filling. These defects not only have an aesthetic impact but also affect the function of the sockets.
By comparison, identifying some of the defects, particularly the surface defects on the front side, with the naked eye required considerable concentration by a person and turning the socket to several angles. Even so, the result was often not flawless. The software required significantly less time to identify the defects, including handling, and achieved 100% results.
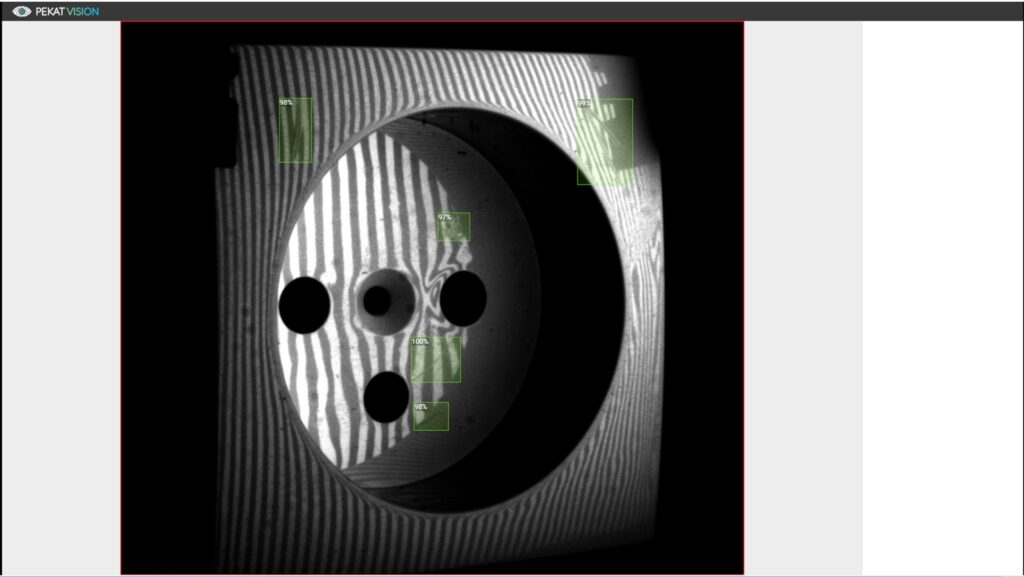
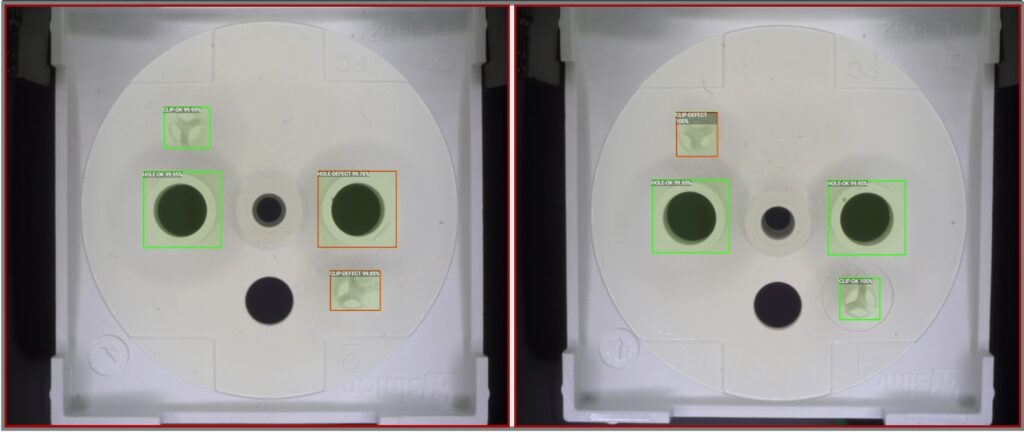
The entire inspection set-up consisted of two Datalogic industrial cameras, a SmartView structured and low angle ring lights, PEKAT VISION software and the MX-G2000 industrial computer. Object handling was provided by a FANUC CRX-5ia lightweight collaborative robot. The PEKAT VISION Surface Detection module was used to inspect the front side of the socket, Detector and Classifier modules for the back side of the socket.
Inspection by an Arm-mounted Camera Robot
In situations where the object to be inspected is too large, complex, or heavy to be handled by the collaborative robot, mounting the camera on the robot arm itself provides a solution. The robot arm with the camera then moves along the object and takes images from predefined positions and angles. Adjusting the arm movement for optimal image capture can be done very easily using manual guidance, so-called drag & drop programming.
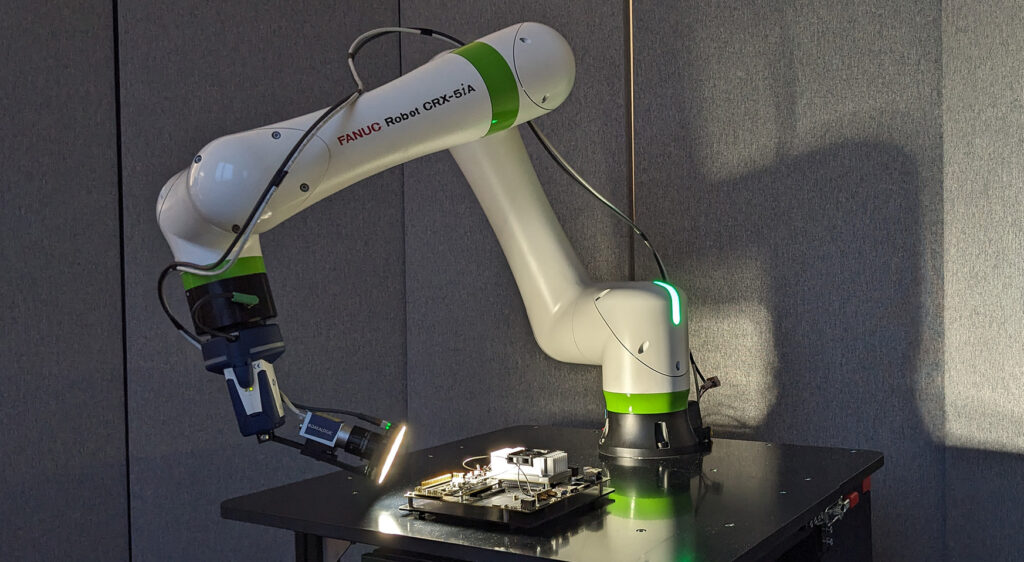
Here, PEKAT VISION chose to check the components of a graphics card. The movement of the camera arm was adjusted using manual guidance to achieve optimal images for the inspection of the selected components. The setup was similar to the previous one, but the ring lighting and camera were mounted directly on the robot arm.
The PEKAT VISION modules Detector and Classifier were chosen for the component inspection. Unlike the Anomaly Detection module, which is trained only on images without defects, these modules require annotation of individual images. The annotation is done in a user-friendly interface of the PEKAT VISION software using a mouse.
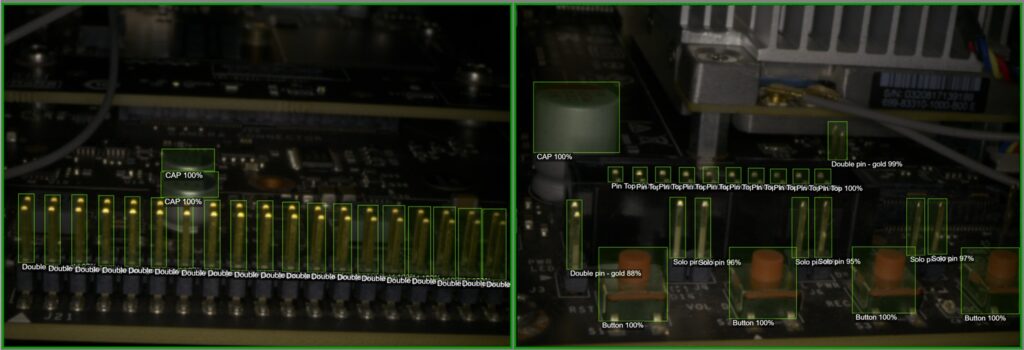
Our demonstration once again showed the ease and reliability of visual inspection using PEKAT VISION software and the simple setup and precision of movements of the FANUC collaborative robot. The arm-mounted camera robot thus significantly expands the possibilities for automating quality control for many other, usually more complex, heavier or larger products. The FANUC collaborative robot portfolio includes robots with a maximum load capacity of 4 kg up to 50 kg and a maximum reach of up to 1889 mm.
If you would like to check whether PEKAT VISION is suitable for your particular need, please, contact us or request a free demo or feasibility study.