In manufacturing, quality inspection is a critical process to ensure products meet specified standards and to reduce defects. Machine vision systems play a pivotal role in automating this task. There are two primary approaches to machine vision: traditional (rules-based) and deep learning-based. Understanding their differences, advantages, disadvantages, and specific use cases can help manufacturers choose the most suitable method for their needs.
Traditional (Rules-Based) Machine Vision
Traditional machine vision relies on predefined rules and algorithms to analyze images. These systems use techniques such as edge detection, pattern matching, color analysis, and thresholding. The process involves selecting the appropriate set of features and setting specific parameters that the system uses to evaluate whether an item meets quality standards.
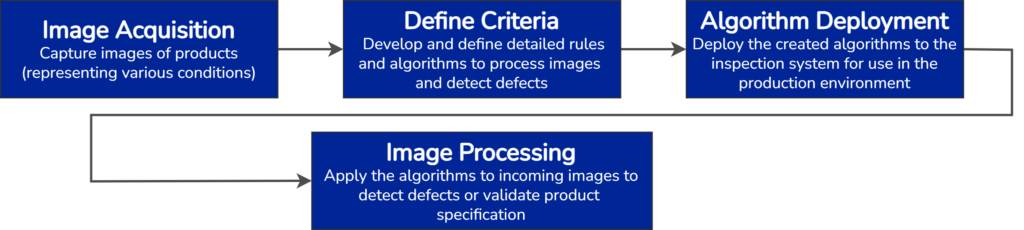
Deep Learning-Based Machine Vision
Deep learning, a subset of machine learning, uses neural networks with multiple layers to automatically learn features from data. These methods excel in complex and varied inspection tasks. Deep learning techniques can be broadly classified into supervised and unsupervised methods.
Supervised methods are trained on labeled datasets to identify and classify images, objects or defects, or extract text from images.
Unsupervised methods are trained using only good images to identify deviations from the norm, indicating defects.
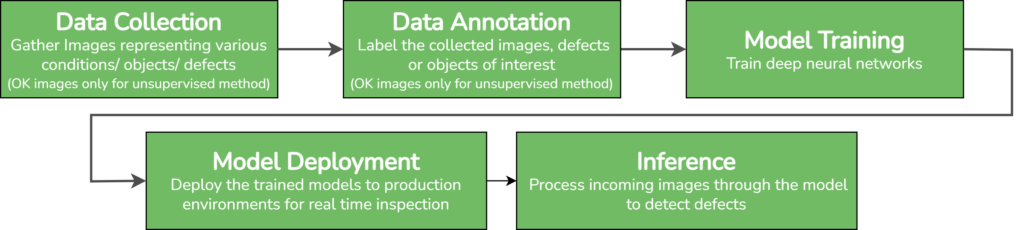
Which Machine Vision Method to Choose
Choosing between traditional machine vision and deep learning for quality inspection in manufacturing depends on several factors, including the complexity of the inspection task, available data, and computational resources. Both approaches are complementary, often working together to provide comprehensive solutions.
Factors to Consider
Task Complexity: Use deep learning for complex, variable tasks; traditional methods for simpler, well-defined tasks, including gauging and measuring.
Data Availability: Deep learning typically requires more data, but for some applications, a very small dataset may suffice. Nonetheless, traditional methods can generally work with fewer samples since rules and criteria are predefined.
Real-Time Requirements: Traditional methods are inherently faster because they rely on predefined rules and algorithms that require less computational power.
Deep learning can be optimized for real-time performance with sufficient computational power, such as using specialized hardware or smart cameras with powerful GPUs. It is suitable for applications where complex analysis is required but processing speed can be balanced with computational resources.
Cost and Resources: When comparing the cost and resources required for implementation and maintenance, it is essential to consider both the hardware and the expertise needed.
Traditional Machine Vision typically involves lower initial hardware costs. However, it demands significant expertise in creating and managing rule-based algorithms, which can be very time-consuming.
In contrast, deep learning generally requires higher initial costs due to the need for powerful computational hardware. Despite this, the requirements for cameras, lighting, and lenses may be less stringent.
Advanced deep learning software like PEKAT VISION significantly reduces the time needed for training neural networks. The process is mostly automated, allowing employees to focus on other tasks once the data is provided. PEKAT VISION’s intuitive interface further simplifies use, virtually eliminating the need for specialized deep learning expertise. Consequently, deploying and operating the software on the factory floor is both straightforward and efficient.
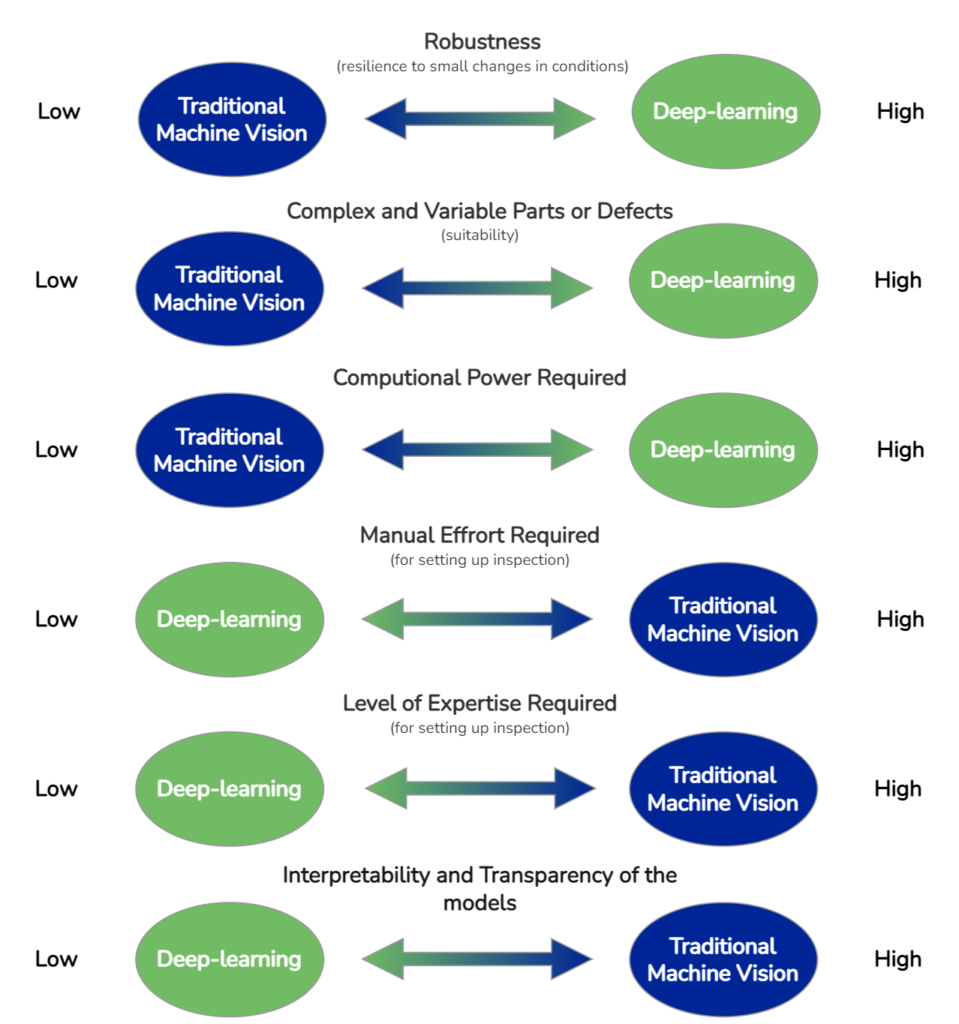
Where Traditional Machine Vision Excels:
Precise Measurement and Gauging: Excellent for applications that require exact measurements of components or distances.
Part Location and Alignment: Ideal for ensuring components are correctly positioned and aligned in assemblies.
Color Analysis: Effective for tasks that involve differentiating products or parts based on color.
Object Location: Suitable for identifying and locating objects within a predefined area.
Code Reading: Highly efficient at reading 1D and 2D barcodes, QR codes, Matrix codes and other symbologies.
Image Preprocessing: Performs well in preprocessing tasks like filtering and enhancing images to improve inspection accuracy.
Where Deep Learning Excels:
Surface Inspection: Excels at detecting complex surface anomalies and textures that are difficult to define with rules.
Object Detection and Classification: Superior in identifying and classifying various objects or defects in diverse and variable conditions.
Anomaly Detection: Capable of learning from normal (OK) images and identifying deviations that indicate defects, useful in applications where defects are rare and varied.
Optical Character Recognition (OCR): Highly accurate in recognizing and extracting text from images, even in challenging conditions like varied fonts or distortions.
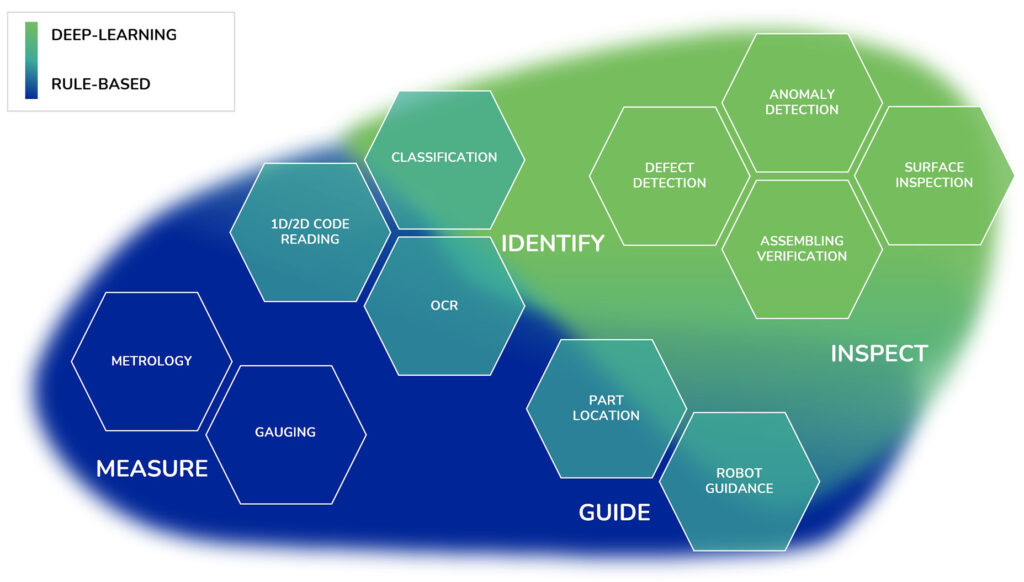
Leveraging Both Methods
In many cases, the best solution involves integrating both traditional and deep learning methods to leverage their respective strengths. For instance, an industrial computer like the MX-G2000 can support both approaches, providing a versatile platform for various machine vision applications. This integration ensures high accuracy and efficiency in quality inspection, allowing manufacturers to achieve superior results.
Both traditional rule-based machine vision and deep learning-based approaches offer valuable tools for quality inspection in manufacturing. By understanding their unique advantages and limitations, manufacturers can make informed decisions on the best approach or combination of approaches to use for their specific needs. This hybrid strategy can lead to more robust and effective inspection systems, ultimately improving product quality and production efficiency.
If you would like to know what is the best solution for your particular application, please, contact us or request a free demo or feasibility study.