For suppliers of reusable drinkware, cup cleanliness inspection is a critical part of the quality control process. At European music festivals, catering companies and their suppliers need assurance that each plastic cup used to serve beverages meets the highest cleanliness standards and is the correct type.
By ensuring the reuse of cups, this process significantly reduces single-use plastic waste, supporting a more sustainable approach to beverage service at large-scale events. After each event, thousands of returned cups are washed and then need to undergo an efficient cleanliness inspection to detect any defects or contaminants. To meet this demand, a company tasked with providing festival cups turned to us at PEKAT VISION for a comprehensive solution.
Scope of Inspection Task
We were tasked with inspecting two types of cups:
- Branded beer cups in two sizes (250 ml and 350 ml)
- Unbranded matte cups in three sizes (S, M, and L)
Our goal was to identify any cup that needed removal from the production line due to the following issues:
- Incorrect cup type or mismatched logo
- Scratches
- Broken edges or cracks
- Attached stickers
- Dirt or contamination
The cups are transported in groups of three on a conveyor belt, rotating to allow inspection from all angles, with a time limit of 100 milliseconds per cup for the inspection process. Here’s how we approached the solution.
Step-by-Step Solution Using PEKAT VISION’s Modular System
One approach was to use the PEKAT VISION Detector and Classifier modules to identify and classify individual defects. However, given the variety of potential defects and their shapes, we opted for a more streamlined approach. While this may seem complex initially, it ultimately proved the most efficient solution.
- Cup Positioning with the Detector Module
First, we used the Detector module to identify the top and bottom of each cup on the conveyor belt, creating a precise reference for each cup’s location. (Figure 1) - Bounding Box Creation with the Unifier Module
Next, we applied the Unifier module to generate a bounding box around each cup. This allowed us to crop the image within the bounding box for focused inspection. This step worked effectively across both cup types and all sizes. (Figure 2) - Defect Classification with the Classifier Module
Finally, we employed the deep-learning Classifier module, training it on two classes:- OK class for images containing the correct, undamaged, and clean cups
- NOK class for images showing any defects or contamination
The Classifier then evaluated each cropped image as a whole, assigning it to either the OK or NOK class based on the presence of any defects or contamination. (Figure 3).
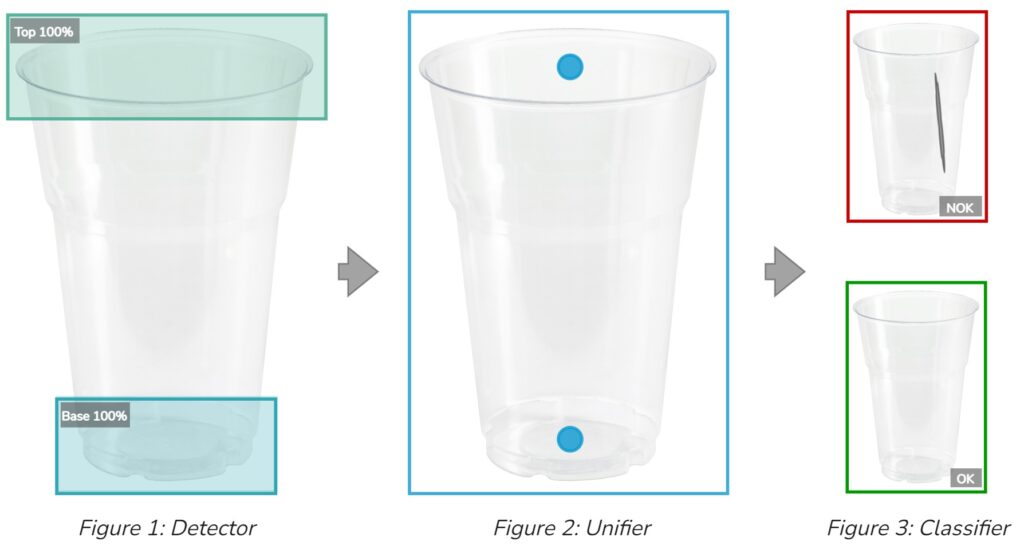
This setup allowed the model to accurately classify each cup well within the 100-millisecond time constraint demonstrating the flexibility of PEKAT VISION’s modules, which seamlessly work together to set up even complex inspections with ease.
Beyond quality control, PEKAT VISION contributes to environmental sustainability by enabling efficient reuse of drinkware, reducing plastic waste, and promoting a circular economy. With our technology, we’re proud to support solutions that combine precision and eco-conscious practices.
Explore More Applications of PEKAT VISION in Quality Control
PEKAT VISION’s modular system makes it versatile across various industries. Learn how our technology aids in PCB recycling or toy manufacturing box cleanliness inspections. Or, if you have unique inspection requirements, reach out to us to discuss a free feasibility study with your samples!